エブリイになんとか可変式2段ベッドを搭載できないか考える記事の第6回です。
前回記事に引き続き、とりあえず手を動かしながら製作を進めていきます。
なんとか綺麗に完成するよう頑張るます。
追記)決定版の記事が出ました。
天板作成
第5回記事で天板に使う合板のカットまで済ませたので、本記事はそこからの続きです。
切り出したままの合板は割とささくれているので、手にトゲが刺さりたくない方は予めサンドペーパーで表面や断面を滑らかにしておきましょう。
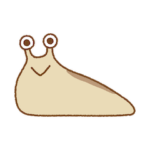
なめくじは先にペーパーを当てました
本格派の方は更に着色したりニスを塗ったりなどお好きにどうぞ。
さて改めまして、今回用意した合板のサイズは以下の通りです。
- 12mm厚:幅730mm×長さ720mm、幅650mm×長さ710mm
- 9mm厚:幅730mm×長さ930mm、幅650mm×長さ800mm
このサイズに合わせてウレタンスポンジと表面材である合皮をカットしていきます。
ウレタンスポンジは元々決めていた製品を、悩んでいた合皮も予算内(1370mm×2,000mm×2ロール=¥4,000)の製品が見つかりました。
これら含め、天板作成には以下の材料を使います。
- パイプ(切り出し済み)&ジョイントパーツ
- 合板(切り出し済み)
- ウレタンスポンジ(35mm厚)
- 合皮
- ビス(ネジ径4.4mm以下、長さ12mm程度)
- ウレタン用ボンド100ml
- タッカー
- サンドペーパー
- カッター/ハサミ
- ドライバー(可能ならインパクト)
- 下敷き用段ボール
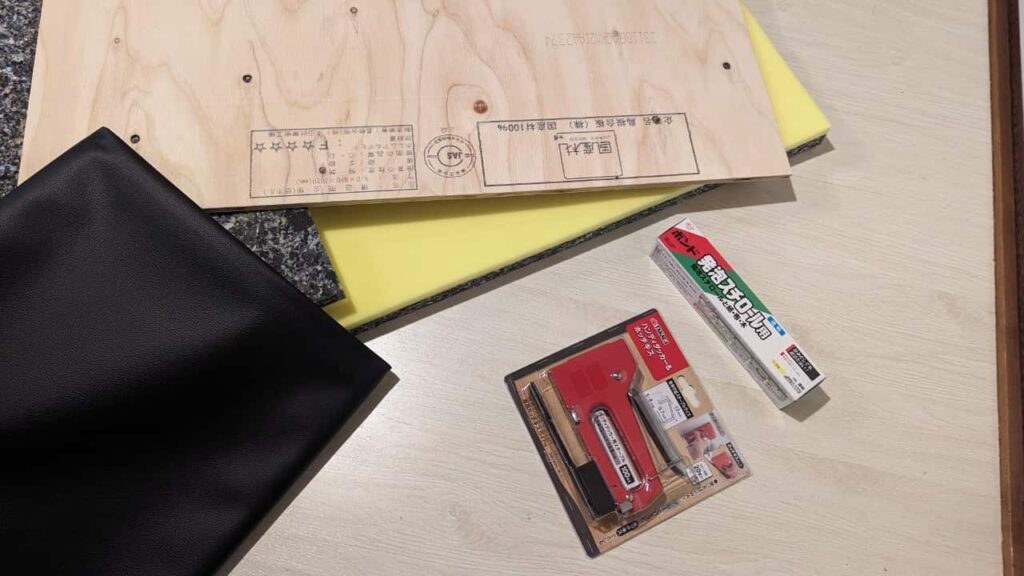
ウレタンスポンジを切り出す
購入したウレタンスポンジは最初から2層構造になっている製品で、試しに寝転びましたが適度なクッション性で快適です。
さて今回は節約のため、全ての天板分のスポンジを購入した2,000mm×1,200mm1枚で賄います。
よってウレタンスポンジは、幅730mmの合板2つ分を先に1枚もので切り出し、残骸から幅630mm2枚分を適宜切り出して組み合わせます。
計算とカット
今回は以下のようにカットしていきます。
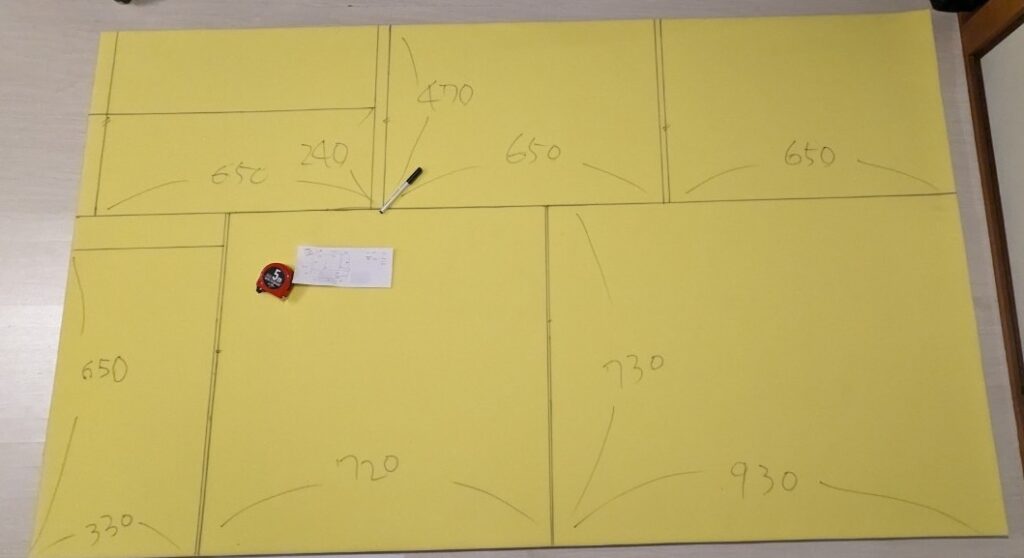
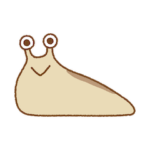
合板を載せてペンで縁取りします
ちなみにウレタンスポンジをちょっとだけ広めにカットして、少し潰すように表面材で巻くと皺が寄りにくいみたいです。
ウレタンスポンジを切るのに使うのは、普通のカッターで大丈夫です。
柔らかい1層目を先にカットし、その隙間をガイドに硬めの2層目を切ってください。
※切る時は段ボールを敷くのを忘れずに!
ウレタンスポンジの接着
首尾よくスポンジがカットできたら、次は合板への接着です。
木とウレタンスポンジはどうも「木工用ボンド」だと接着できないようなので、ウレタン用ボンドで貼り付けていきます。
ガチガチに接着する必要はないため、今回の面積で使うボンドの量は、1枚につき100ml入りチューブの1/4〜1/3程度です。
合板に適当にかけてからヘラで伸ばし、数分程度の硬化時間を待ってからウレタンスポンジを貼り付けていきます。
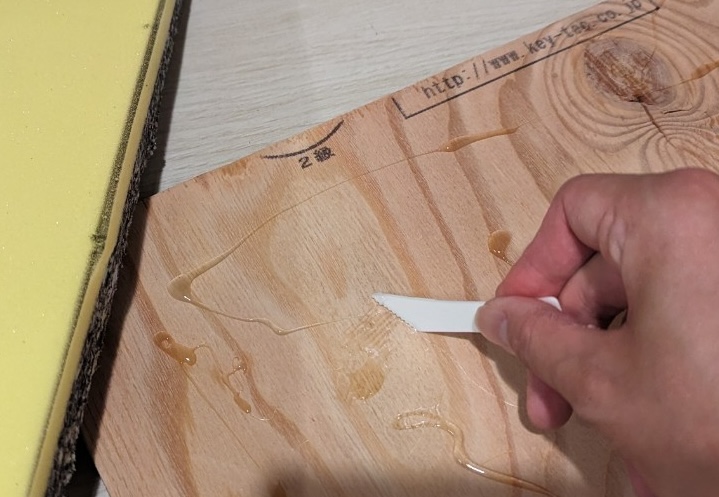
箱の説明通りに、ある程度の時間が経ったらしっかり踏みつけて固着させます。
合皮のカットと留め
今度は合皮をカットしていきます。
ウレタンスポンジと違ってツギハギすると都合が悪いので、1枚ものとして切り出していきます。
天板とスポンジの厚みが合計44〜47mmなので、天板の長さ+天板厚50mm*2+留め代50mm*2くらいあると良さそうです。
今回購入したのは巾1,370mm×2,000mm×2ロールなので、以下の通りで切り出します。
- 650mm+200mm=850mmを2枚
- 730mm+200mm=950mmを2枚
合皮を切り出したら合板+ウレタンスポンジを包み、留め代分の生地を必要最低限にトリミングします。
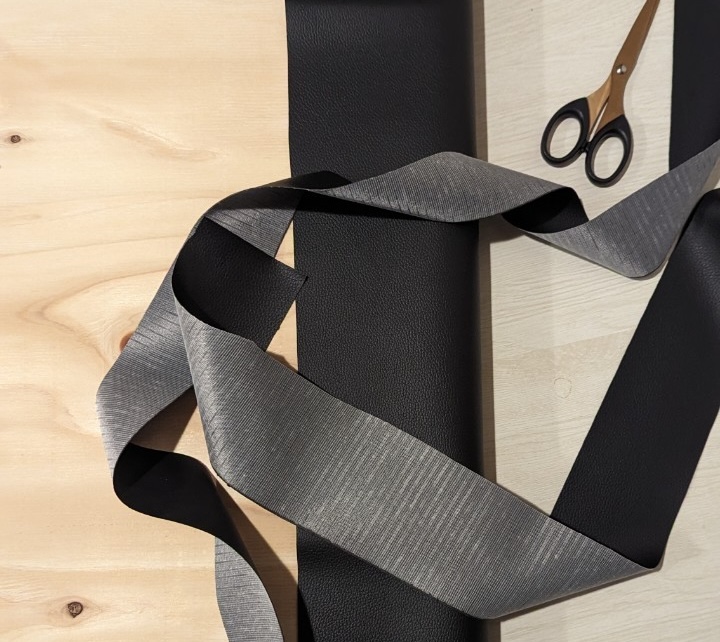
後はタッカー留めをひたすらしていきます。
タッカー留めは簡単にやるのであれば裏側のみ、合皮をピン張りにしたい方はサイド→裏側の順に生地を引っ張りながら留めていきましょう。
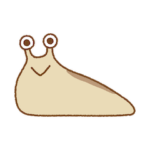
サイドの留めも合板を狙って打ち込みます
※ちゃんとしたやり方はResta様の記事を参照してください
角は適当に余りを切除して処理していきます。
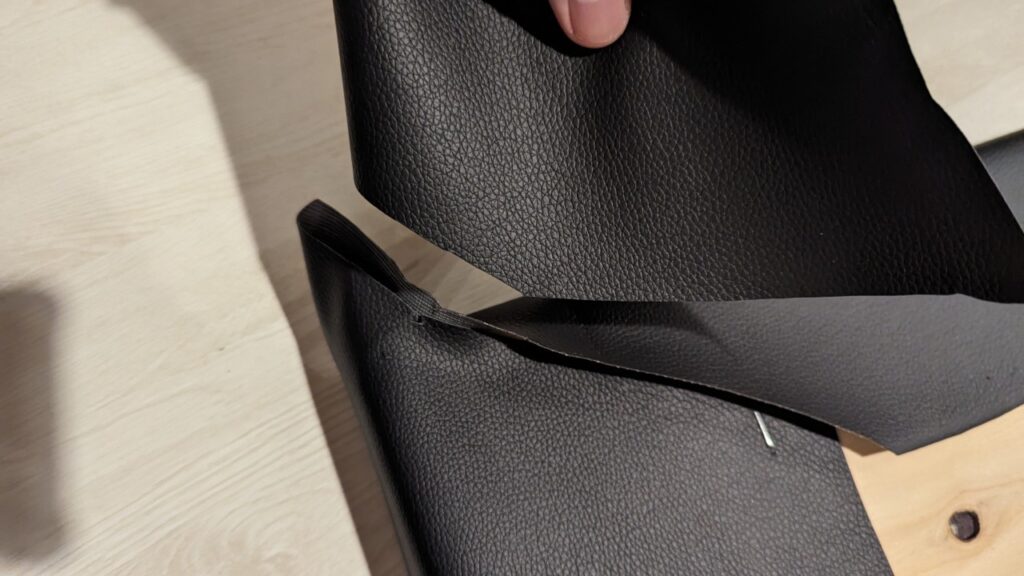
タッカー留めの間隔は5cm刻み程度、4枚分で合計400〜500本は針を使います。
パイプの接着
天板にウレタンスポンジと合皮が貼れたら、最後にパイプを接着していきます。
さてパイプ(鉄+プラ塗装)と合板(木)をどうくっつけるかですが、この素材同士は接着剤だとまともにくっつきません。
よって計画通り、ジョイントパーツを使ってパイプを固定していきます。
使うのはJB-46およびJ-46と、それに見合う数の直径4.4mm以下/長さ12mm程度のビスです。
長さは16mmくらいまではいけると思いますが、長いビスだと合板を貫通してウレタンスポンジ層に数mm飛び出すことを理解しておく必要があります。
さてビス打ちの位置決めですが、まず天板無しの状態でベッドフレームに必要なジョイントパーツを付けておきます。
そこへ天板を載せて位置決めをした後、裏側からジョイントパーツ位置の微調整をします。
そしてパーツ位置が決まったらビスをガンガン打ち込んでいきます。
ビス打ちにはインパクトドライバー使用が楽ですが、大した長さや数じゃないので普通のドライバーでなんとかなります。
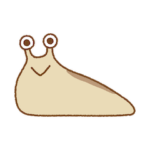
ネジ穴をナメないように注意です
またベッド→ソファモードへの切り替えの際、フレームへ天板を引っ掛けられるようにするため、追加でジョイントパーツを取り付けていきます。
安定性や取り回しによってジョイントパーツの個数が変わるため、こちらは接着せず、個数も天板1枚につき2個としておきます。
動作チェック
天板が完成したら、改めてモード切り替えを含む様々な動作チェックをします。
モード切り替えについて
実際に確認したところ、プラスチックパーツの接合力が強すぎて、モード切り替えが結構大変であることが分かりました。
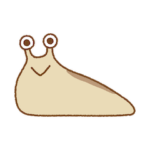
天板を外すのにハンマーが欲しくなるレベルです
よって、J-13B/JB-13B、J-59C/JB-59Cの接合部を若干トリミングして、あえて接合力を弱めます。
この時、過度にトリミングをすると安定感が落ちたり、外れる危険性が出てくるので注意が必要です。
パーツの買い直しになるとダルいので、パイプの端材などで結合部の加減を確認しながら慎重に作業していきます。
なめくじが行ったのは「接合部裏側にある窪み線に沿ったトリミング」で、丁度いい加減の接合力になりました。
ちなみにジョイントパーツをトリミングするには、DIY用の細ノコが便利です。
※プラ用カッターはイマイチでした
伸縮部について
伸縮部は角度などの条件で滑りが悪くなる場合あるので、念の為に全てシリコンスプレーを振っておきます。
またリアシート復元テストでフレームとシートの干渉が発覚したため、Φ32mmのパイプを5cm程度切断することにしました。
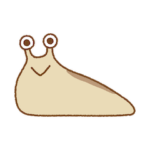
あれだけ長さを確認しながら作業したのに…
安定感について
パイプとジョイントパーツを接着していない段階では、実用レベルの安定感ではありません。
正直言って、かなり揺れます。
よって、一番外側の直方体フレームの角は後述の接着が必須です。
ただし接着するとモード変更やメンテナンスに不都合が出る箇所の接合については接着無しとします。
さて必要な箇所を接着したらそれなりに実用的なレベルの安定感になりました。
それでも強度に不安な場合は、ラッシングベルトや結束バンドなどを使ってフレームを壁面側に固定しておくと安心ですね。
なめくじは100均で子ども用のベルトを2本購入して、以前設置したバーと結束しました。
パーツ接着
動作チェックを入念に済ませ、問題が無いようであれば、先々のメンテで取り外しが必要がないパーツへサンアロー接着液を流し込んでいきます。
さてここで問題なのがサンアロー接着液の使い勝手です。
デフォルトでパイプの隙間に流し込む用の器具が同梱されていますが、ハズレ製品を引いたのか手元で漏れ出して使い物になりません。
あれこれと接着方法を試しましたが、結局一番間違いないのは接着液を指で塗ることです。
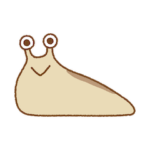
指が嫌な方は細いハケや綿棒を束ねたものを用意しましょう
具体的には接着液を指やハケなどでパイプとパーツ内壁へ十分量を塗布して、即座に捻じ込むのが理想です。
接着液はかなり即効性・速乾性があるため、1分くらい固定すれば最低限は固まります。
さらに隙間を塞ぐようにスポイトか醤油差しなどで追い塗布ができると最高です。
接着液をパイプに塗ると表面のプラ加工がすぐ溶けてドロドロになるため、液ダレに注意したり、汚れた手でその辺を触らないようにしましょう。
接着がうまくいけば1日のうちにガッチガチに固まります。
一気に接着を終わらせようとせず、何点かずつに分けて作業するのがお勧めです。
最後に
本当はこれで可変式2段ベッドの自作シリーズを終わらせたかったのですが、1回実地テストをしてみないと不安な出来です。
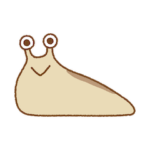
早くしないと夏になっちゃう…!
なのであと1記事だけ、自作シリーズは追加となります。
改めての紹介や作り方については、それとはまた別の記事でまとめます。
しかし自作して痛感しましたが、ややこしい機構のベッドを作るのは中々大変です。
お金がある方は、信頼できるビルダーへ相談して作ってもらうのもありだと思います。
おそらく製作費に20〜30万円程度はかかるでしょうが…
貧乏性のなめくじは自作したってだけです、なぜなら自分で作れば工賃タダだから!
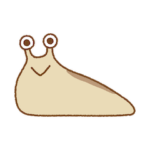
ではまた次の記事でお会いしましょう